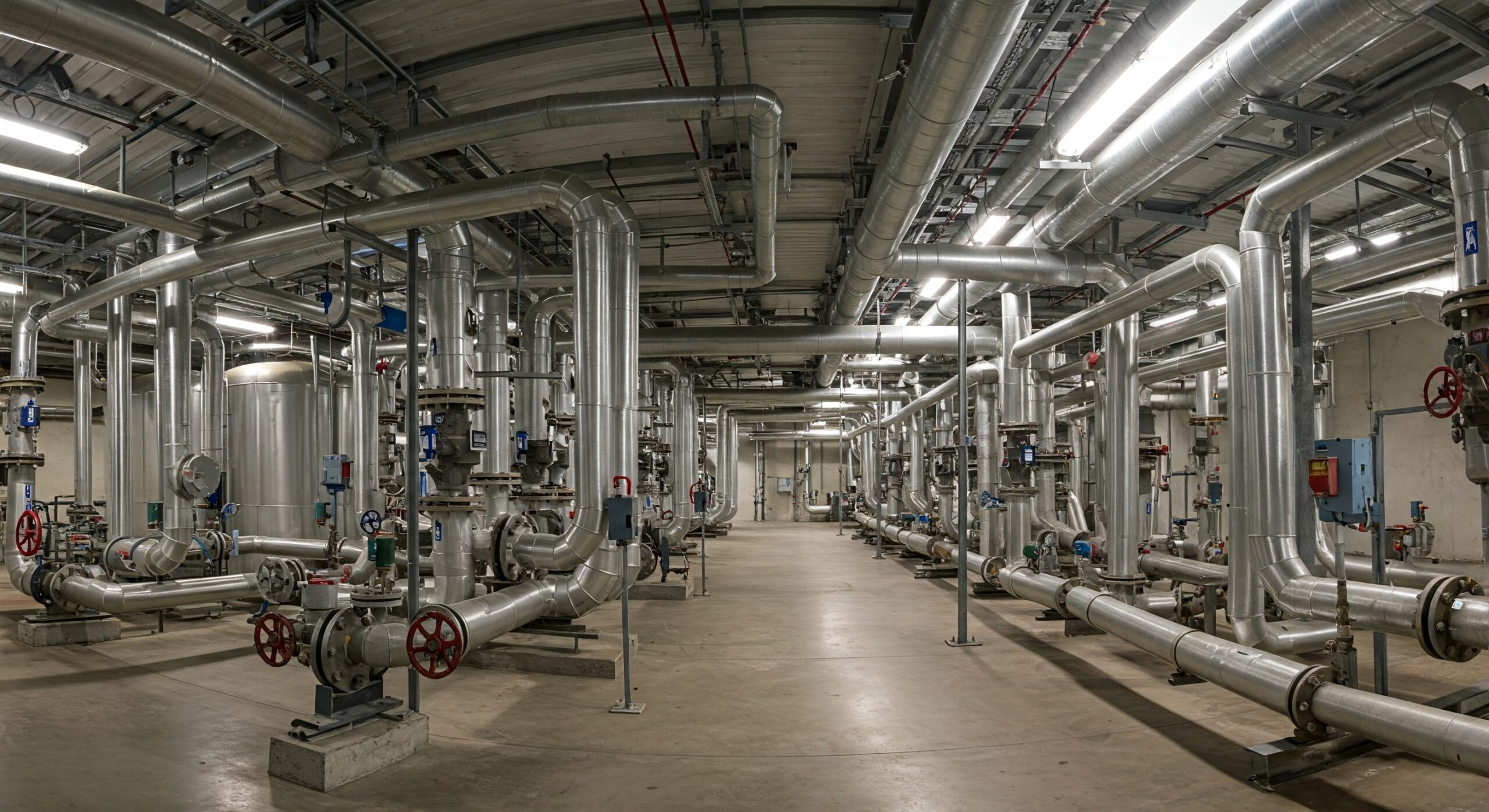
Renewal Asset Management Program (RAMP)
Often, facility condition assessments drive capital plans but don’t link up with an execution strategy. RAMP executes capital plans with fully developed deferred maintenance projects based on performance-driven assessments.
What an actionable deferred maintenance program can do for you
For Facility Leaders
- Asset assessments based on condition, rather than age
- Component-level maintenance and renewal recommendations
- A project list with scopes of work to refurbish or replace unstable assets
- Project work managed by Halcyon’s PM staff to ensure deficiencies identified in the assessments are addressed correctly during the project
For C-Suite Leaders
- A capital renewal strategy that integrates refurbishment and replacement investments to maintain business continuity in the most economic and time-effective manner
- Benchmark deferred maintenance by asset type and by building to compare needs across your portfolio and to track stabilization status over time
Benefits of the Renewal Asset Management Program (RAMP)
Spend Wisely
Integrate refurbishment projects at a fraction of replacement project costs
Execute Projects Faster
Reduce project schedules and outage disruption
Increase Volume
Execute more projects within a capital budget and fiscal year
Traditional Facility Condition Assessments
Assessments
Lifecycle modeling and unit cost estimates generate need
Outcome
Deferred maintenance need is presented to leadership for funding
Where Traditional FCAs Stop
Where Traditional FCAs Stop
Deferred Maintenance Execution
Halcyon’s Performance-Driven Assessments
Examples of Component-Level Field Observation Procedures (Air Handling Units) | |||
---|---|---|---|
Component | Procedure | Component | Procedure |
Supply Air Fan | Accessible (Y/N) DA Static Pressure Setpoint DAT Setpoint (on BAS) Design Discharge Air Volume (CFM) Observe Bearing Temperature Observe Belt Condition Observe DA Static Pressure Observe Discharge Air Temperature (DAT) Observe Fan Speed (hz) Observe Moisture Levels in Fan Chamber Observe Motor Data Plate / Presumed Age Observe Noise / Vibration Motor Starter: Accessible (Y/N); Observe Condition VFD (if applicable): Accessible (Y/N), Observe Alarms, Observe Filter Condition, Observe Status | Controls | Observe if Graphics Exist on BAS Observe DA Temperature @ BAS Observe DA Temperature @ Duct Observe RH @ BAS Observe RH @ Supply Duct Observe SP @ BAS Observe SP @ Supply Duct |
General Conditions | Accessible (Y/N) Epoxy Treatment (Y/N) Cleanliness Observe General Condition of Insulation Observe General Condition of Piping Observe Location/Condition of CHW Strainer Observe Location and Condition of Valves Structural / Airtight Integrity UV Light Assembly |
Deferred Maintenance Project Identification
AHU Component | Component Impact Weighting | Component Condition | Stabilization Score (Impact * Condition) | Findings | Recommendations |
---|---|---|---|---|---|
Supply Air Fan | 30 | 80% | 24 | Motors from 1986. No soft starts. Static pressure control via vortex dampers (actuators in process of being replaced); fan 1 welds visible from previous metal repairs on fan structural support members. Fan 2 housing is cracked. Missing hardware on main shaft pillowblock bearing – likely vibration issue. | Demo both supply fans and install fan array. |
Cooling Coil (CC) Assembly | 25 | 100% | 25 | CC fouled with biologic growth; condensate carry over upstream of coil causing growth in discharge plenum; coil fins disintegrating; structural framing members corroding. | Clean strainer; engineer a replacement cooling coil solution and replace coils. Replace existing 3-way chilled water control valve with 2-way. |
Hot Deck Coil Assembly | 20 | 60% | 12 | Moderate level of debris in coil. HW control valve needs adjustment for proper indexing with commands (deadband of no movement between ~80-100%). | Cooling coil and heating coil are contiguous in same plane. Replace heating coil when cooling coil is replaced. Replace 3-way heating water control valve. |
Filters | 5 | 60% | 3 | Prefilters heavily loaded in center at OA intake. | Center filters take the dirtiest air from the OA intake, consider replacing interior prefilters more frequently. |
Condensate Drain / Pan | 5 | 80% | 4 | Condensate drain pan is heavily fouled and rusted. Matting material is saturated holding water and allowing growth of biologics. Trap concealed under unit. | Remove matting. Clean/abrade floor. Coat and seal with epoxy. Clean drain line and begin PM procedure to treat with condensate pan biocide product. |
Dampers | 5 | 80% | 4 | OA damper is not controlled via BAS or AFMS and has no actuator. Galvanized damper surround is corroding and failing allowing air bypass around damper through bulkhead. Bird screen is clogged with debris. | Demo damper and holding frame/galvanized steel plenum wall. Work with TAB to set OA damper to appropriate levels (via calculation OA is 43%). Replace bird screen @ intake. |
Controls | 5 | 60% | 3 | Hot deck temp sensor reading low; INET server and TAC controllers obsolete with no ability to modify graphics or control logic. No safeties (high static, end switches, etc.). | Replace hot deck temp sensor; consider design of new control system/SOO for AHU 1 to include static pressure control to new fan array controller and safeties. |
General Conditions | 5 | 80% | 4 | Piping insulation likely ACM. CHW coil iso valves likely non-op (to individual coils); strainer appears untouched for extended period of time (is overhead difficult to access); rust on bulkheads and floors; abandoned roll-type filter system in place; open j-boxes at vortex dampers; torn flex connectors at SAF discharges (1 and 2); no air mixers; SA plenum (cold deck) very fouled w/ growth. | Consider sampling/abating ACM on hydronic pipe insulation at areas where future disturbance likely; clean/replace CHW strainer; remove abandoned roll filter system; install covers on open j-boxes; replace SAF flex connectors; consider installation of air mixers to help prevent stratification of hot OA at intake; abrade/clean bulkheads and coat w/ epoxy and clean SA cold deck plenum – consider replacement of SA cold deck plenum; replace all doors/access panels and seal all unit section seams. |
79 |
Project Development and Funding
Building | System | Asset | Project Description | Project Budget | Project Duration (Months) |
---|---|---|---|---|---|
Building A | Mechanical | AHUs | Refurbish AHU serving west side, ED & sleep lab | $ 960,000 | 9 |
Building A | Mechanical | AHUs | Refurbish AHU serving east side | $ 785,000 | 9 |
Building A | Mechanical | AHUs | Refurbish 3 AHUs serving 10 operating rooms | $ 1,022,500 | 7 |
Building A | Mechanical | Controls | Create a modern controls infrastructure, purchase IT equipment and install network architecture to integrate into enterprise-wide building automation system | $ 490,000 | 10 |
Building A | Plumbing | Pumps | Replace (1) chilled water pump, (1) domestic water pump, and (2) hot water pumps at end of life | $ 95,000 | 2 |
Building A | Electrical | ATS | Replace (2) obsolete transfer switches serving emergency loads | $ 127,500 | 4 |
Building A | Electrical | Motor Control Center | Replace the motor control center with a main distribution panel | $ 522,800 | 8 |
Building B | Mechanical | Condensate Tank | Replace failed pump packages and perform critical maintenance per manufacturer specifications. | $ 15,000 | 2 |
Building B | Mechanical | Cooling Towers | Refurbish (2) cooling towers and replace (2) condenser pumps | $ 625,000 | 4 |
Building B | Mechanical | Heat Exchangers | Install new flash tank and vent line to safely discharge high pressure condensate and prevent damage to heat exchangers; includes necessary repiping and insulation work | $ 25,000 | 1 |
Building B | Electrical | Electrical System | Replace selective electrical equipment including busways, distribution panels & starters | $ 2,585,800 | 13 |
Building C | Mechanical | Steam Generators | Replace steam generators and install automated blowdown | $ 120,000 | 2 |
Building C | Electrical | Electrical System | Replace existing switchboard and panel EDP | $ 433,000 | 2 |
Building D | Mechanical | Boilers | Recommission boiler flue exhaust system | $ 125,000 | 2 |
Building E | Plumbing | DW Heat Exchangers | Replace (2) domestic water heat exchangers, failed valves & repair associated pumps | $ 40,000 | 3 |
Project Execution
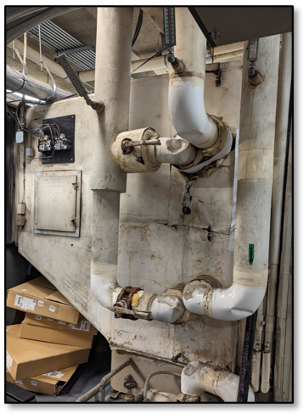
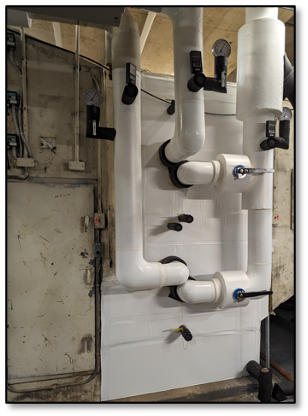
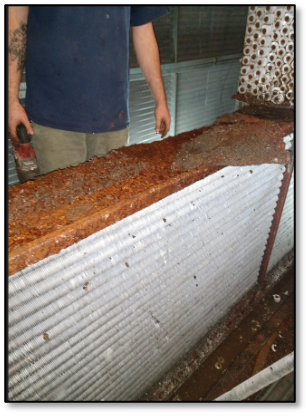
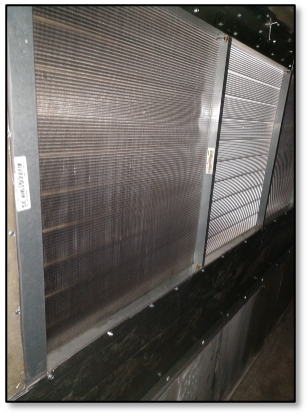
Deferred Maintenance Progress and Reporting
Ramp Inventory | RAMP Stabilization Status | RAMP Reinvestment Recommendations | ||||||||
---|---|---|---|---|---|---|---|---|---|---|
System | Asset | Count | Unstable Assets | % Unstable | FCA Deferred Maintenance | RAMP Project Cost | RAMP Funding Recommendation | Comments | ||
Mechanical | AHUs, Ductwork & Distribution | 12 | 9 | 75% | $ 20,820,224 | $ 4,510,300 | Fund | Refurbish (10) AHUs, resolve downstream distribution & reseal ductwork | ||
Boilers | 2 | 0 | 0% | $ 435,128 | $ – | Do Not Fund | Boilers stable; no recommendations | |||
Heat Exchangers | 3 | 0 | 0% | $ – | $ – | Do Not Fund | Heat exchangers stable; no recommendations | |||
CHW Pumps | 5 | 1 | 20% | $ 187,275 | $ 15,000 | Fund | Replace CHWP 1 | |||
HHW Pumps | 4 | 1 | 25% | $ 111,099 | $ 40,000 | Fund | Replace HHWP 5 | |||
Exhaust Fans | 25 | 0 | 0% | $ 807,112 | $ 10,000 | Fund | Install roof guardrail; Exhaust fans operational; no recommendations | |||
Fume Hoods | 4 | 0 | 0% | $ – | $ 57,000 | Fund | Repair fume hoods | |||
Controls | N/A | N/A | N/A | $ 3,548,782 | $ 490,000 | Fund | Upgrade controls (new front end & tie in critical assets; provide graphics) | |||
Plumbing | DCW Pumps | 2 | 1 | 50% | $ 102,450 | $ 20,000 | Fund | Replace DCWP 1 | ||
Sewer/Sump Pumps | 5 | 0 | 0% | $ 165,753 | $ – | Do Not Fund | Pumps stable; no recommendation | |||
Water Heater | 1 | 0 | 0% | $ 12,473 | $ – | Do Not Fund | Water heater stable; no recommendation | |||
Air Compressor | 6 | 6 | 100% | $ 112,384 | $ 60,000 | Fund | Install rotary air compressors and dryer for control air | |||
Expansion Tank | 6 | 0 | 0% | $ 22,567 | $ – | Do Not Fund | Expansion tanks stable; no recommendation | |||
Plumbing Fixtures (Sinks/Showers/Toilets) | N/A | N/A | N/A | $ 2,729,617 | $ – | Do Not Fund | Defer until future renovations | |||
Distribution | N/A | N/A | N/A | $ 4,323,182 | $ 327,000 | Fund | Resolve findings from pipe scan assessments | |||
Electrical | Switchgear | 2 | 0 | 0% | $ – | $ 46,500 | Fund | Equipment operating; maintenance overdue & requires electrical shutdowns | ||
Main Transformers | 1 | 0 | 0% | $ – | $ 49,500 | Fund | Equipment operating; maintenance overdue & requires electrical shutdowns | |||
Transfer Switches | 9 | 4 | 44% | $ 154,620 | $ 102,000 | Fund | Replace (2) transfer switches | |||
Bus Ducts | 3 | 0 | 0% | $ 2,043,361 | $ – | Do Not Fund | Bus ducts stable; no recommendations | |||
Motor Control Center | 2 | 1 | 50% | $ 495,086 | $ 220,000 | Fund | Decommission MCC & replace with main distribution panel | |||
Transformers/Panels/Breakers | 100 | 0 | 0% | $ 2,373,949 | $ 350,000 | Fund | Recent IR scan deficiencies to be resolved with replacement of OR electrical panels | |||
Emergency Lighting | N/A | N/A | N/A | $ 786,898 | $ – | Do Not Fund | Defer until future renovations | |||
Lighting | N/A | N/A | N/A | $ 5,276,521 | $ – | Do Not Fund | Defer until future renovations | |||
Wiring | N/A | N/A | N/A | $ 2,175,906 | $ – | Do Not Fund | Defer until future renovations | |||
192 | 23 | 12% | $ 46,684,386 | $ 6,297,300 |